樹脂製品の成形不良対策
MKS処理・GMT処理
用途・技術
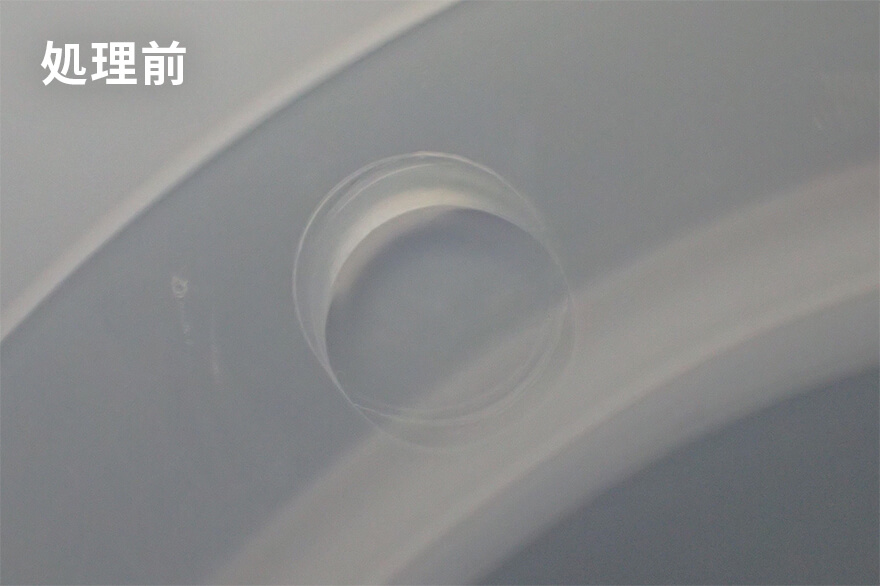
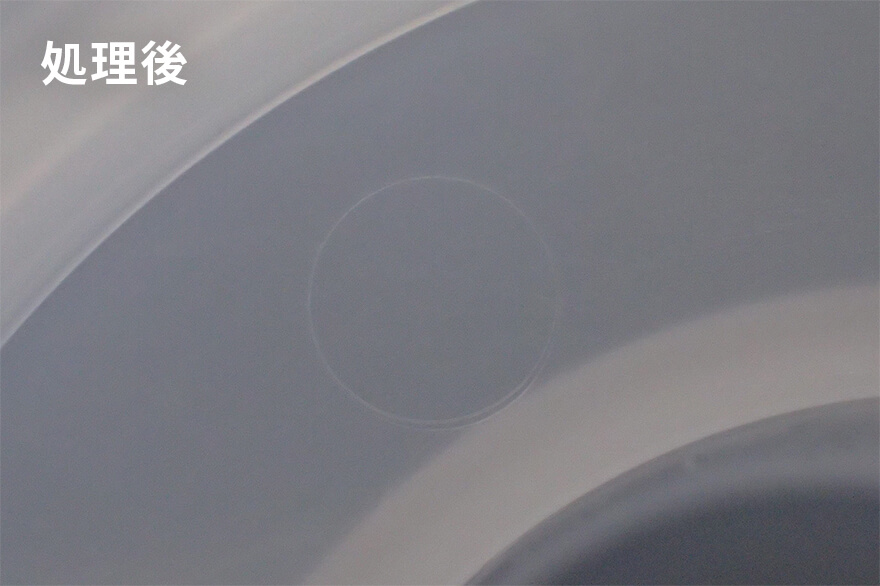
MKS処理® 及びGMT処理による樹脂流れと離型性の向上
樹脂(プラスチック)成形で常に不良なく順調に成形することが出来れば大きなコストダウンと品質向上が実現出来るはずですが、現実には多くの生産現場でヒケ、ウェルドラインなどの樹脂流れに起因する問題やエジェクタピン(押し出しピン)痕のフクレ、樹脂の金型への張り付きによる反りなどの離型性(型離れ性)に起因する問題を解決するために、射出圧力や金型温度などの成形条件調整が日々行われております。
当社では多くの生産現場で課題となっている「樹脂流れに起因する問題」と「離型性に起因する問題」を解決すべく、エアーブラスト技術で金型表面改質を実現するMKS処理®、そしてMKS処理を更に進化させたGMT処理®を開発。当ページではMKS処理及びGMT処理の概要や成形性改善事例などについて詳しくご説明します。
point MKS処理による樹脂(プラスチック)成形の不良対策とは
MKS処理とは、エアーブラスト技術による成形問題解決のための多工程表面処理のことであり、この処理によって作り出されたナノ単位から数μmレベルの均一な凹凸が、流動樹脂と金型表面の接触面積を減らし、樹脂が冷えにくくスムーズな流れを実現する環境を作り出します。
また、方向性のある研磨目は樹脂が収縮の際に抵抗となるが、MKS処理後の無方向性に変更された均一な凸凹表面は前後左右への摺動性が向上し、樹脂収縮時の金型への張り付きを低減させ、離型性を向上させます。
樹脂流れの改善
樹脂が流れやすい環境を作る
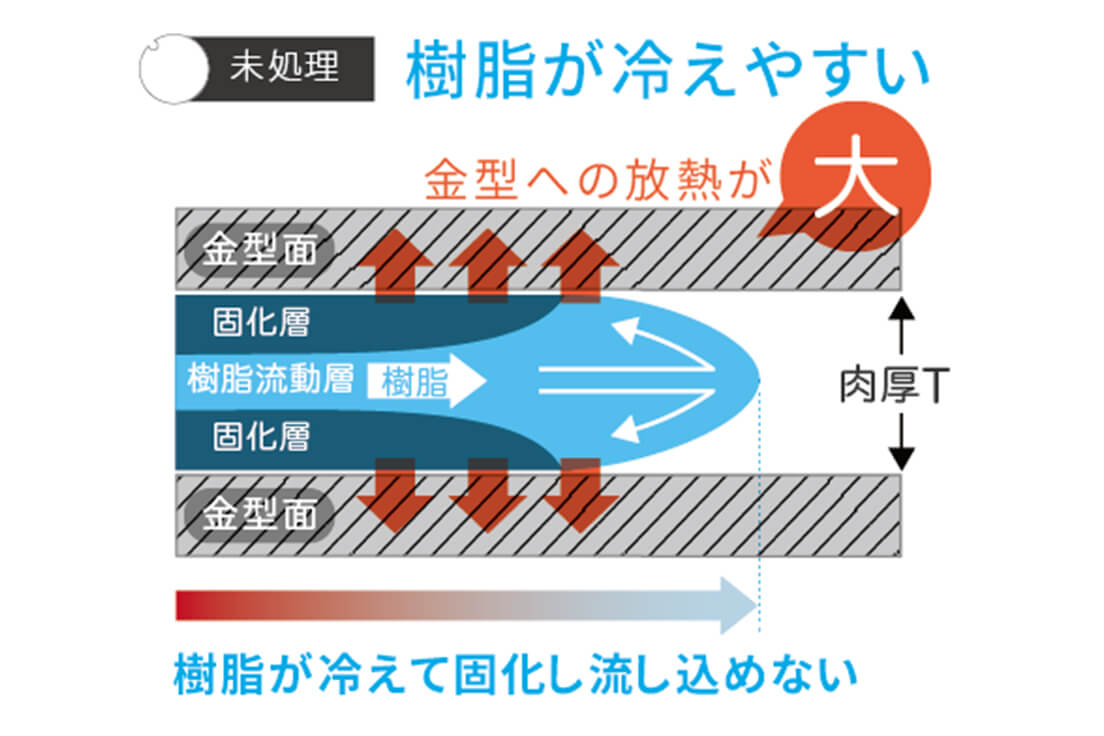
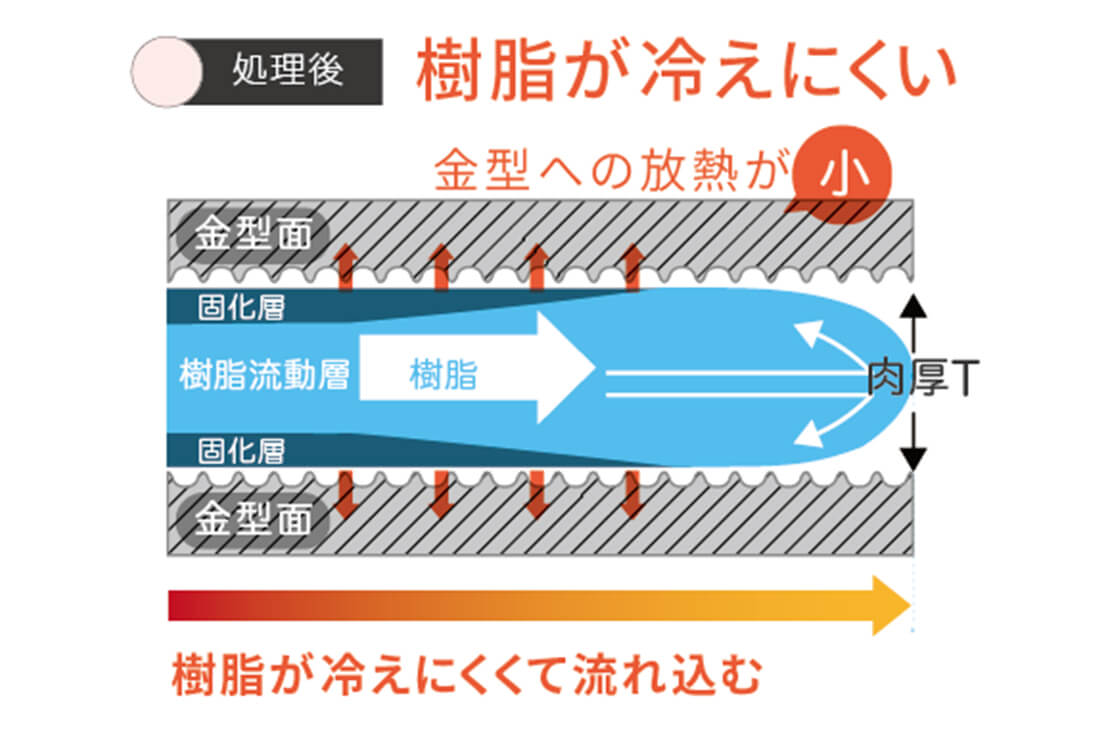
離型性の改善
樹脂の張り付きを低減
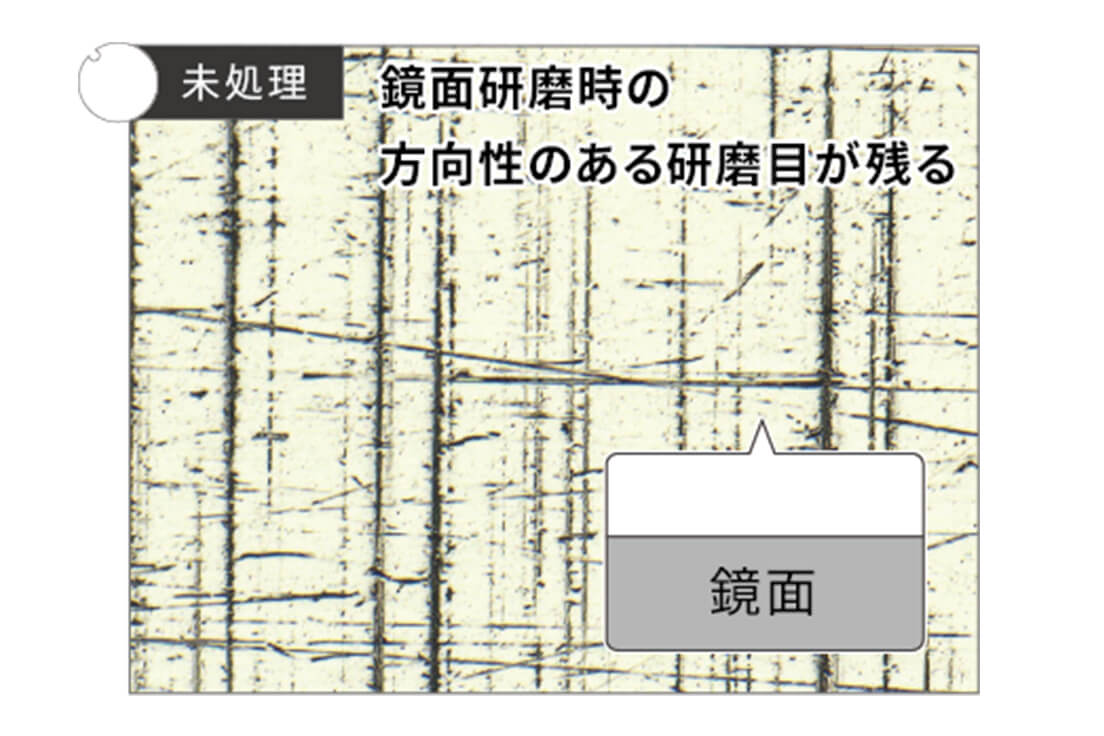
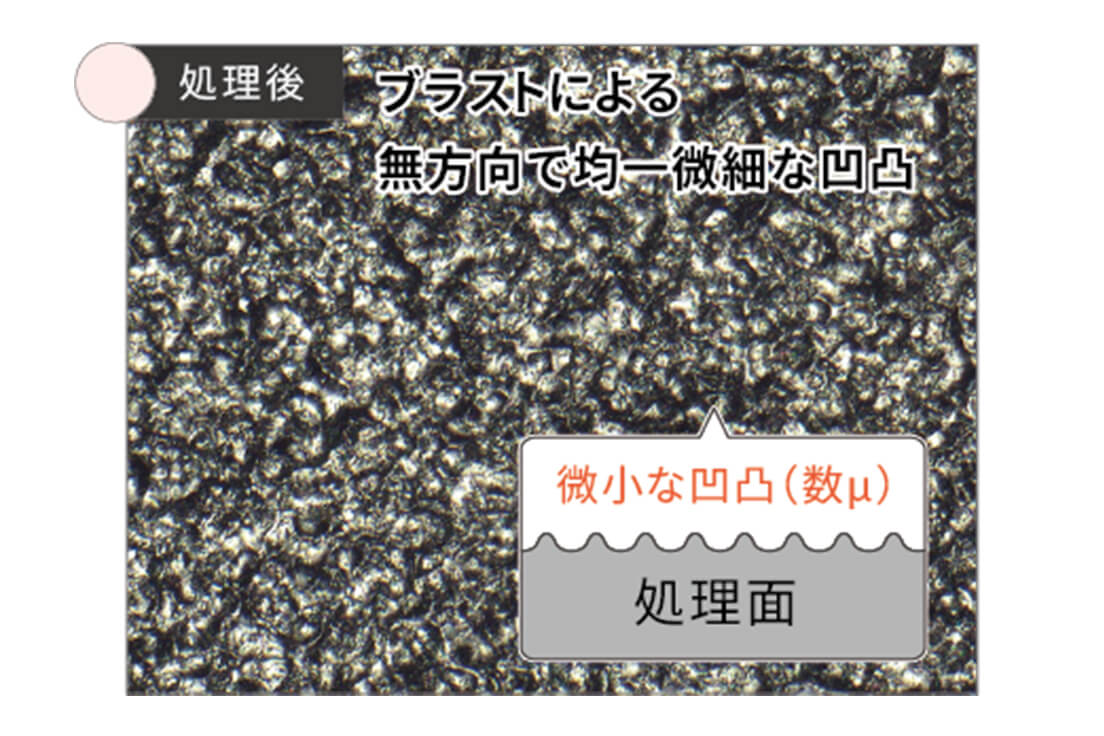
reduction of mold release resistance MKS処理による離型抵抗力の低減効果
抜き勾配ゼロで離型抵抗力が1/5に改善
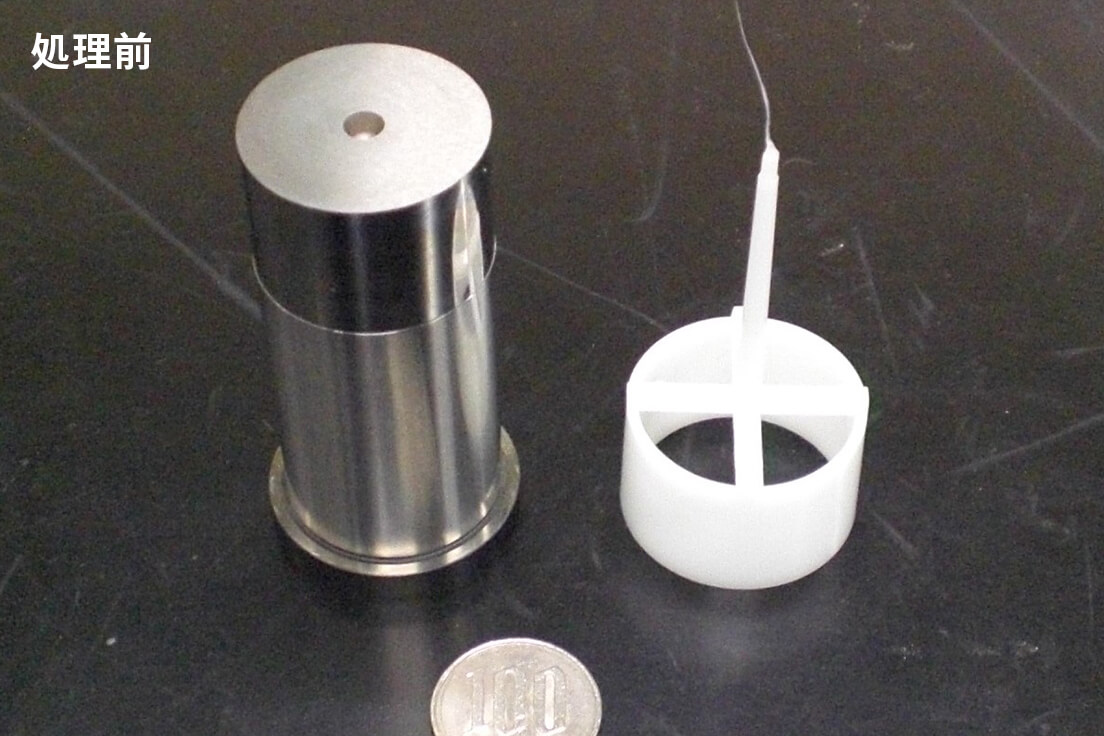
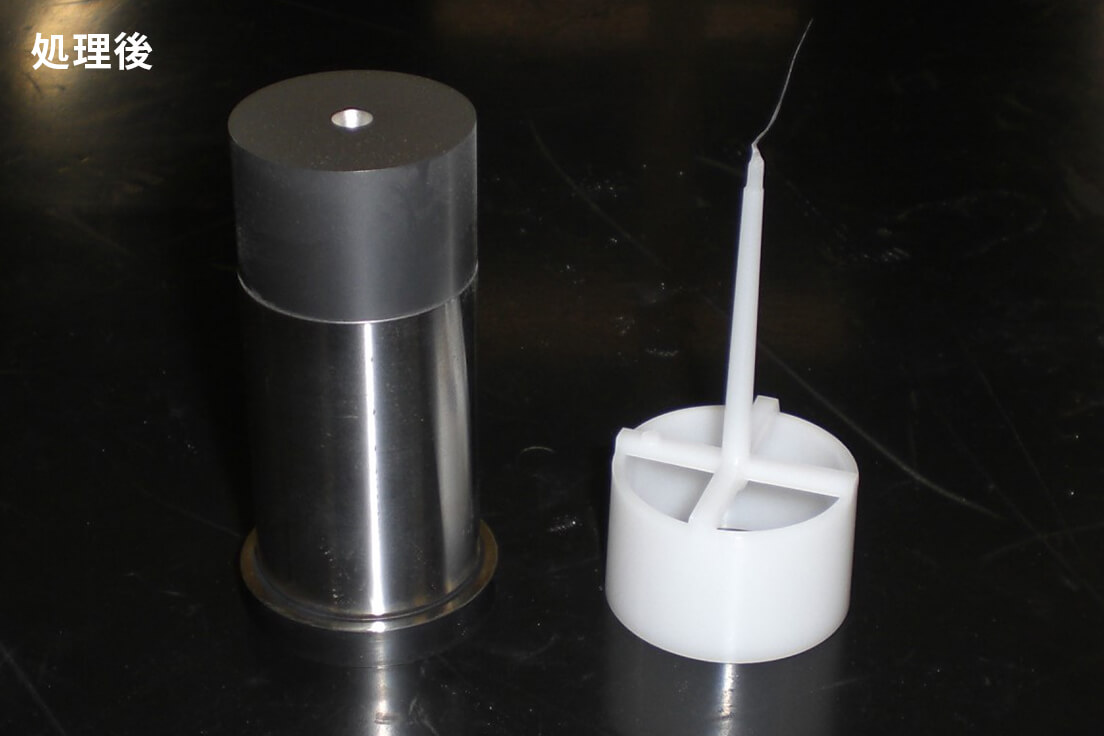
実験金型構造及び測定方法
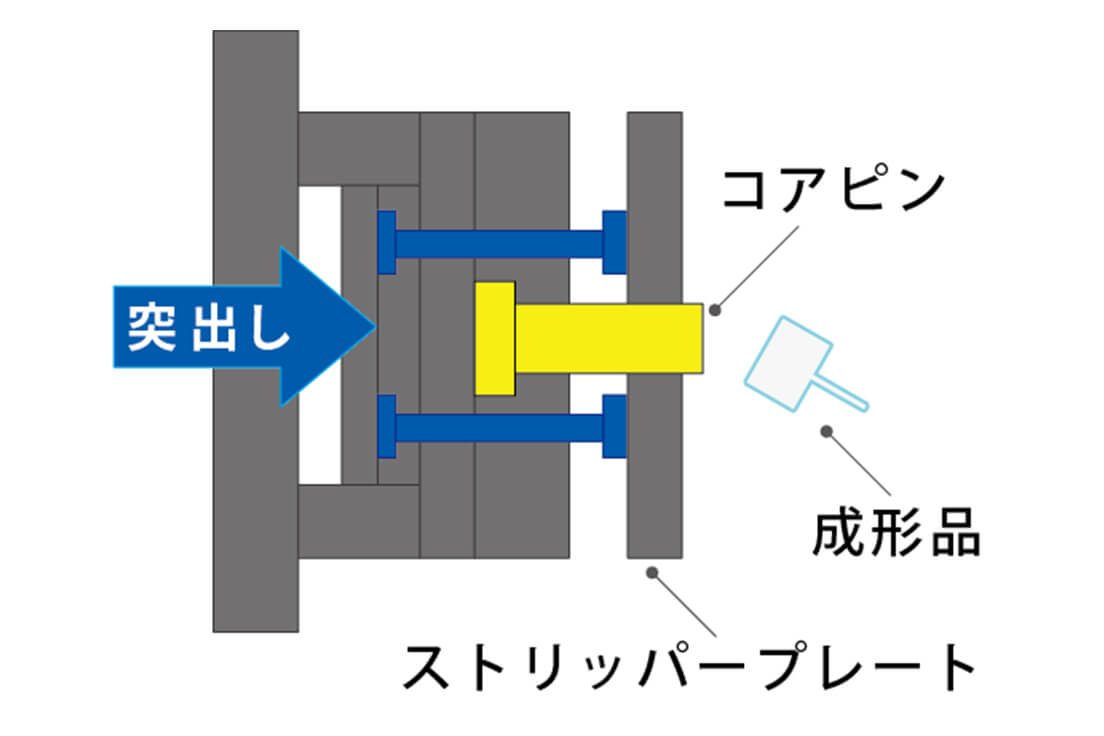
測定方法
センサーにてストリッパープレートを押出す力(≒離型抵抗力)を測定
処理品
コアピン寸法 Φ30×L60mm
成形材料
POM ジュラコンM90-44
サイズ
成形品 Φ30×20H
センサ
水晶圧電式センサー
協力
岩手大学金型技術研究センター
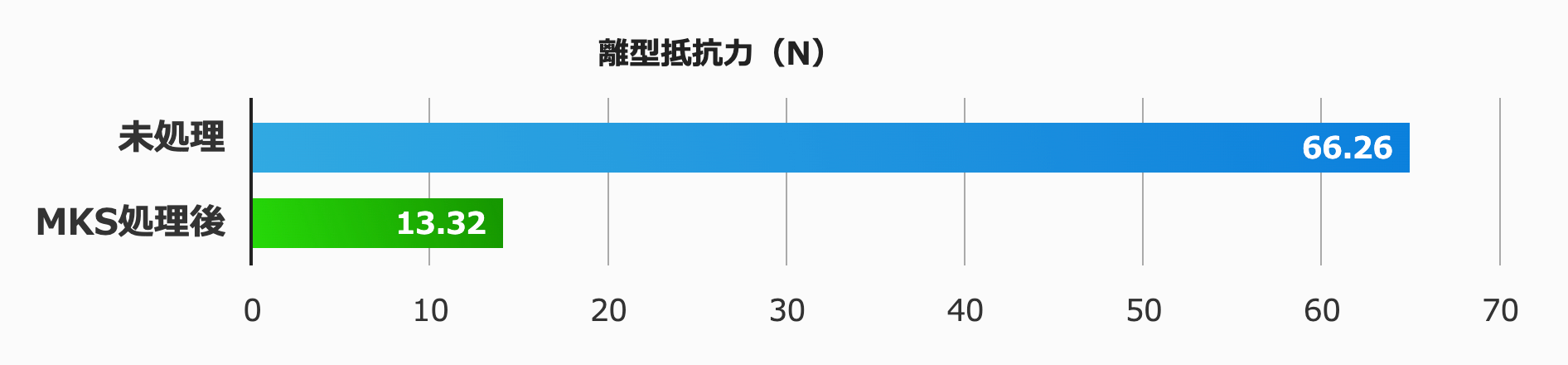
Ra [μm] |
Rz (Rt,Ry) |
Rq [μm] |
RDq | RSk | RKu | |
未処理 (研削加工) |
0.100 | 0.869 | 0.129 | 0.049 | -0.854 | 4.030 |
MKS 処理後 |
0.088 | 0.888 | 0.112 | 0.051 | 0.022 | 3.820 |
resolvable molding defects MKS処理による効果で解決可能な主な成形不良
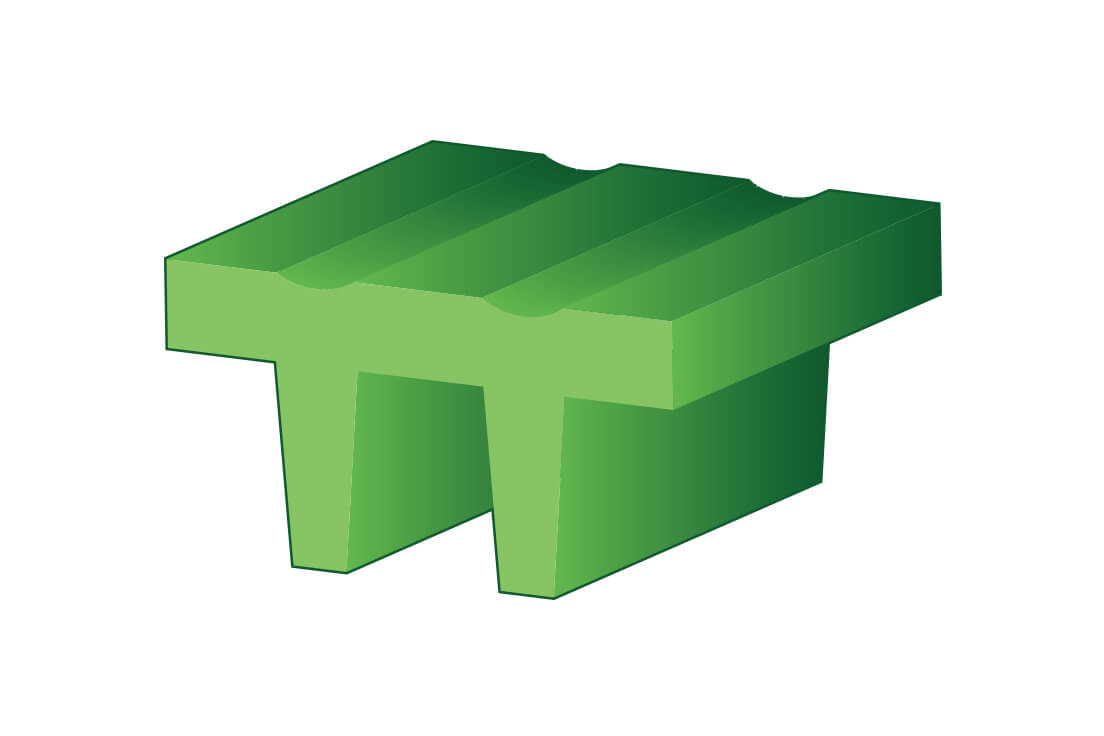
ヒケ
成形品の肉厚部やリブ部に発生する表面の凹みのこと。表面と内部の不均一冷却による樹脂の収縮差が原因。ゲートシール前に充填樹脂量を増やすことが有効。
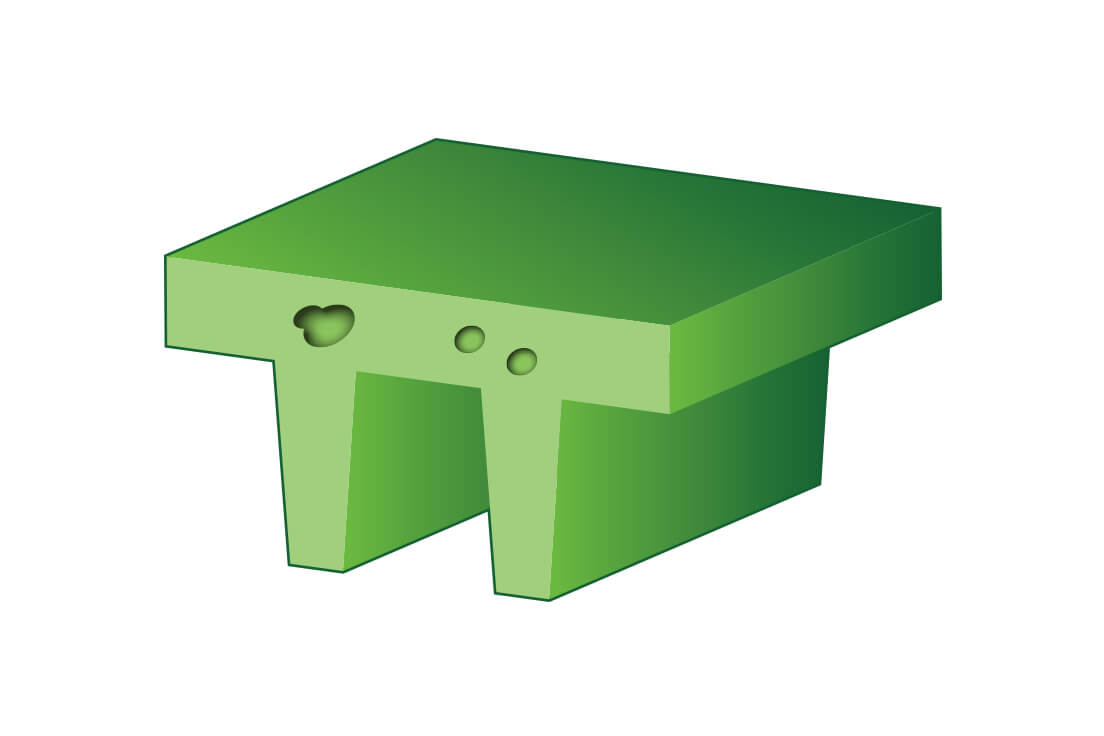
ボイド(気泡)
成形品の肉厚部分に発生する空洞。原因はヒケと同じ。表面に出来るのがヒケ、内部に出来るのがボイド。剛性の高い樹脂はヒケでなくボイドが出来やすい。ゲートシール前に充填樹脂量を増やすことが有効。
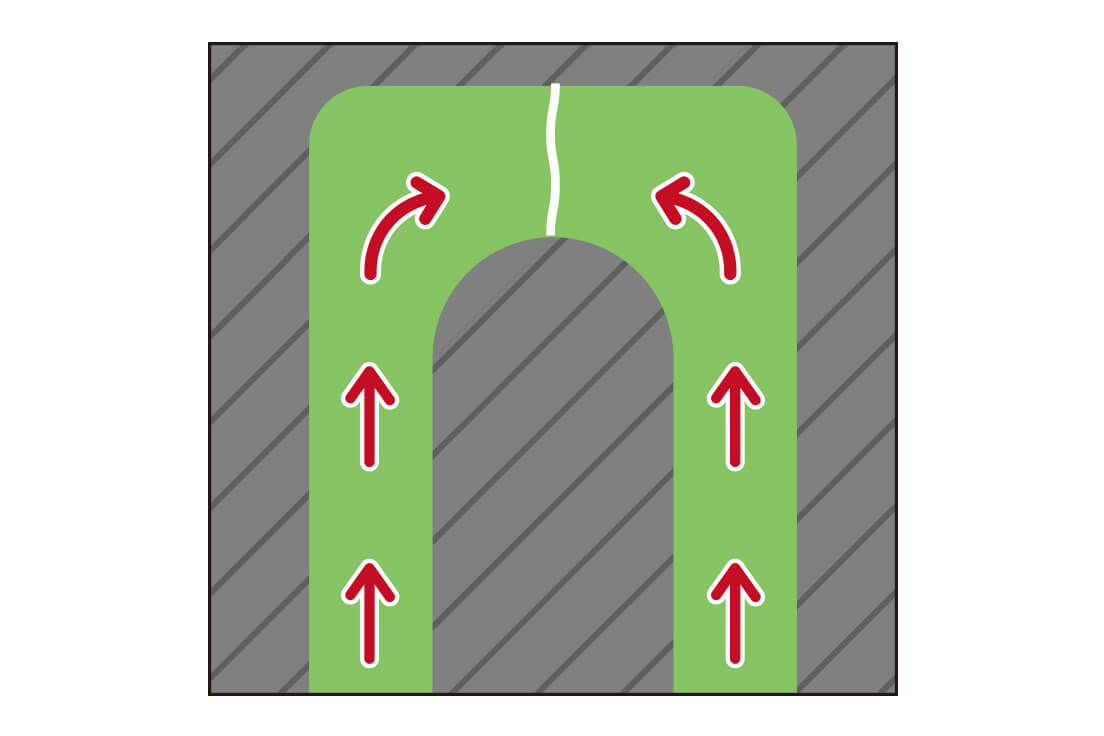
ウェルドライン
溶融樹脂の先端同士が合流する際に、樹脂温度が低くなり過ぎて、既に固化が始まっていることが原因。樹脂の合流部分にウェルドラインと呼ばれる線が残る。
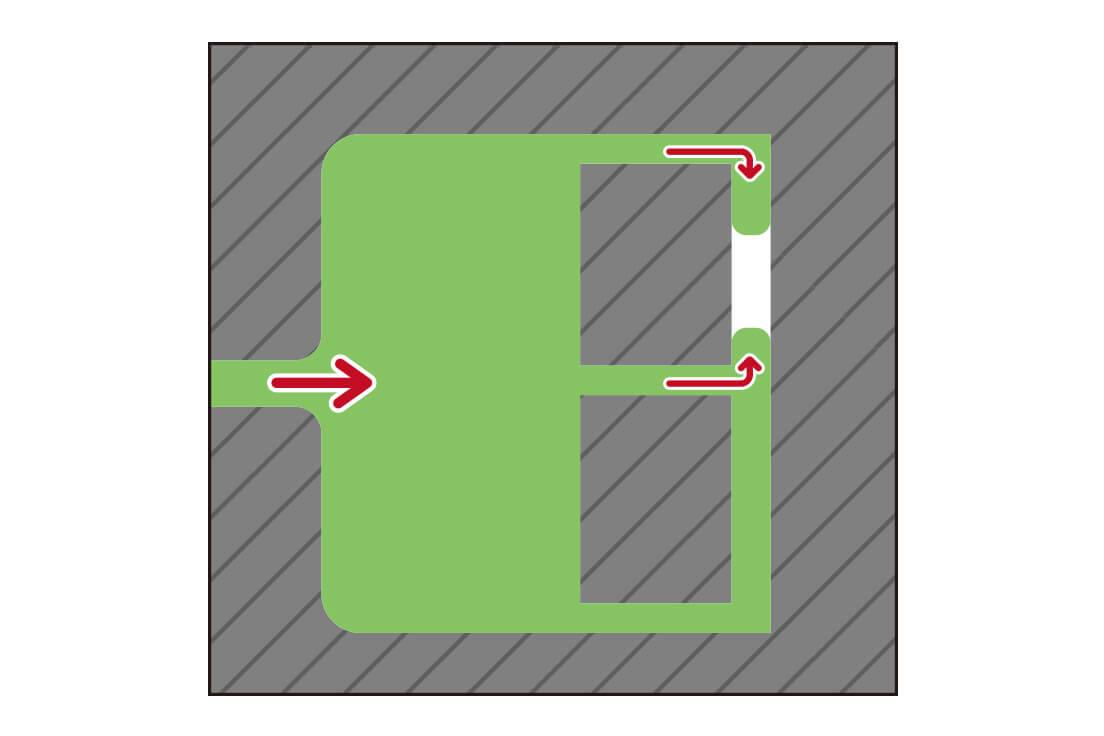
ショートショット
金型内の一部に樹脂が充填されてない状態で冷却、固化した成形品。樹脂の流動性が悪く、金型内の末端まで届く前に冷却され固化しているのが原因。
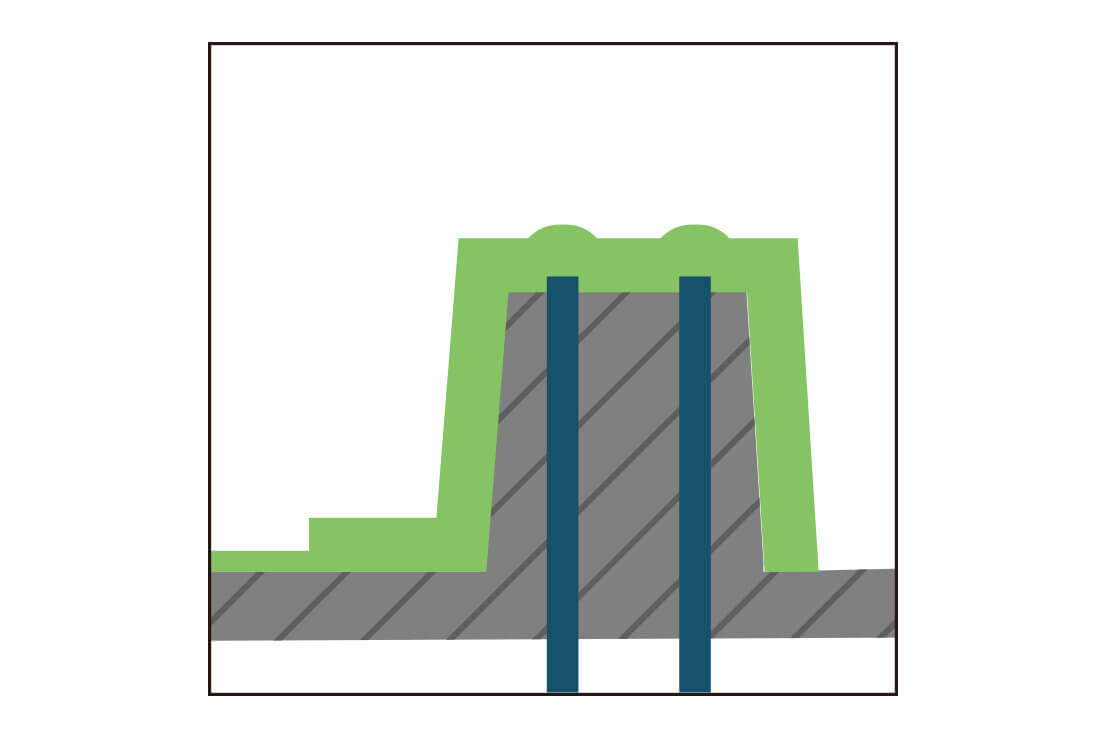
フクレ、クラッキング
成形品が固定側金型や稼働側金型に張り付いてエジェクタピンが成形品を突いて突起を作ったり、ヒビを入れてしまうこと。離型時の抵抗力が大きいことが原因。
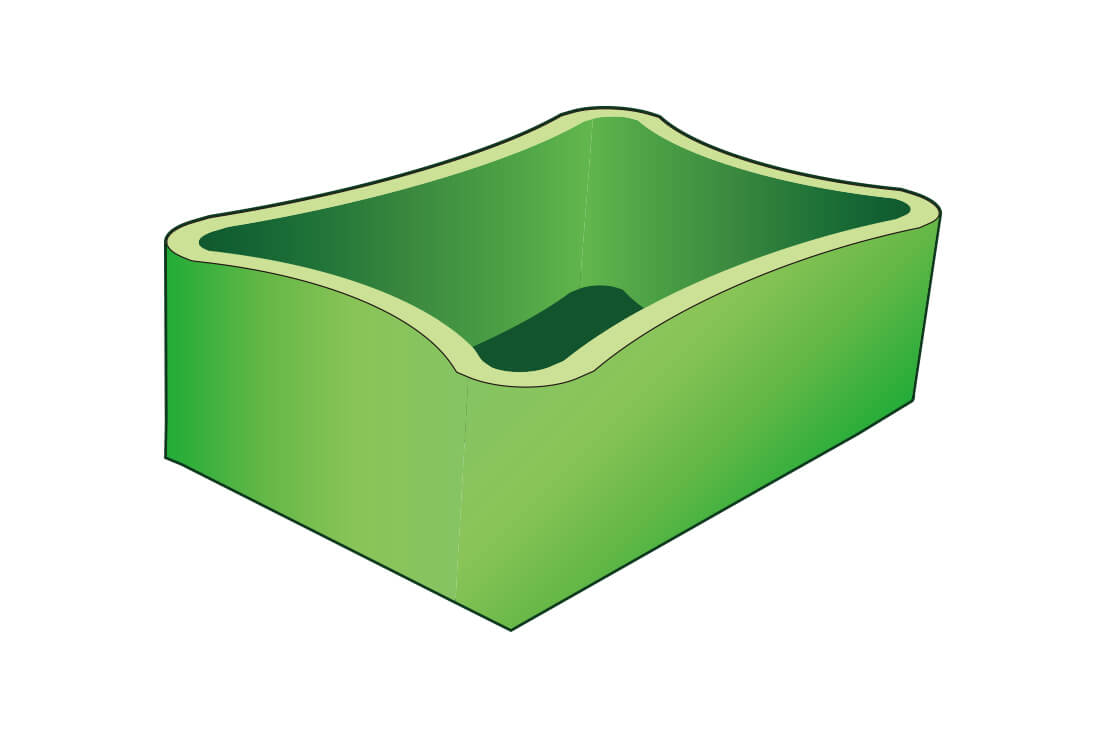
反り、歪み
平板状や箱型の成形品で発生する反り、曲がり、ねじれなどの変形。収縮時の金型への張り付きによる不均一な固化や射出成形時の圧力による残留応力が原因。
- 上記で記載しているMKS処理の効果で解決可能な成形不良とその成形不良原因はあくまで主な一例であり、金型の設計、樹脂の種類、各種成形条件などに成形不良原因とその対策が必要な場合もあります。
エアーブラスト技術による金型やスクリューのクリーニング
当ページでは金型表面改質を実現するMKS処理及びGMT処理による樹脂(プラスチック)成形の不良対策についてご紹介しておりますが、エアーブラスト技術は金型や射出成形機スクリューのクリーニングにも使用されております。
エアーブラスト技術による金型やスクリューのクリーニングは、ダメージレスで高効率であり、細溝やコーナー部のクリーニングも容易です。
molding with high transparency and improved mold release GMT処理による透明度の高い成形と離型性改善の両立
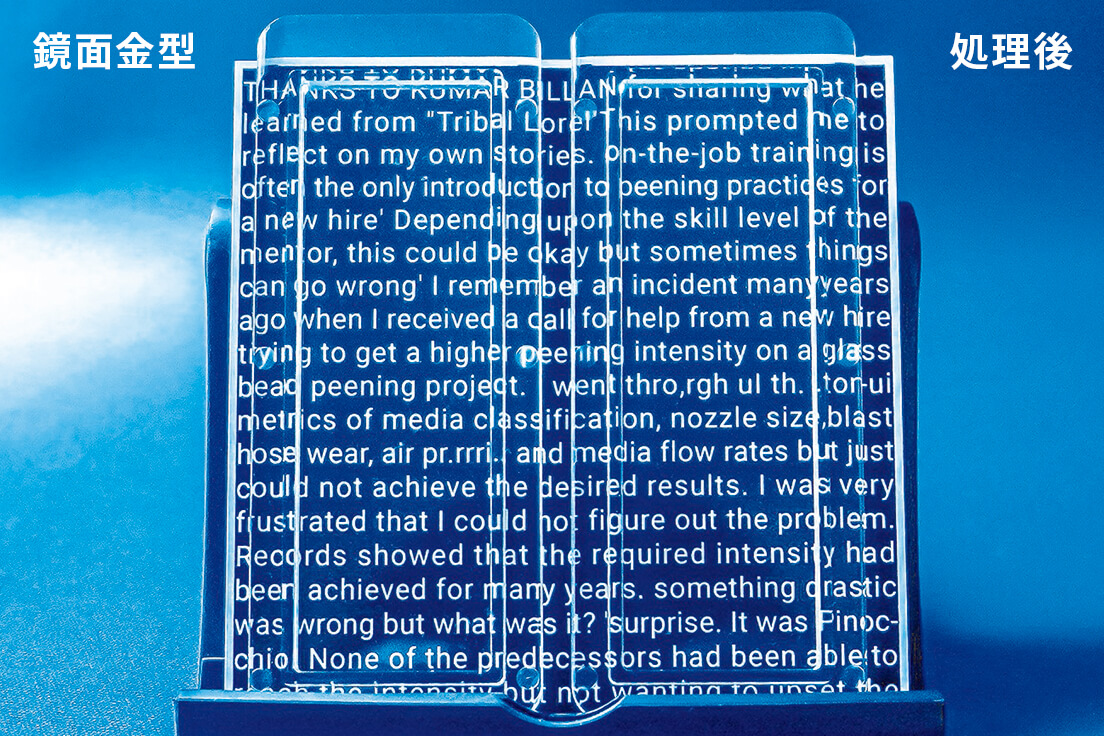
GMT処理とは、離型剤を使わずに透明度の高い成形と離型性改善を両立させた金型表面処理です。右画像は、鏡面仕上げ金型で離型剤を塗布して成形した場合とGMT処理後の金型に離型剤を塗布せずに成形した場合の比較ですが、成形品の透明度は目視では判断できないレベルです。
GMT処理ならば毎回の離型剤塗布の手間とコストを無くしても、従来と同じ成形が出来ることから、透明度の高い樹脂(プラスチック)成形品の多い化粧品関連、医療器具関連などの成形の効率化、低コスト化手法として幅広くご利用頂いております。
技術ポイント(特許登録済み)
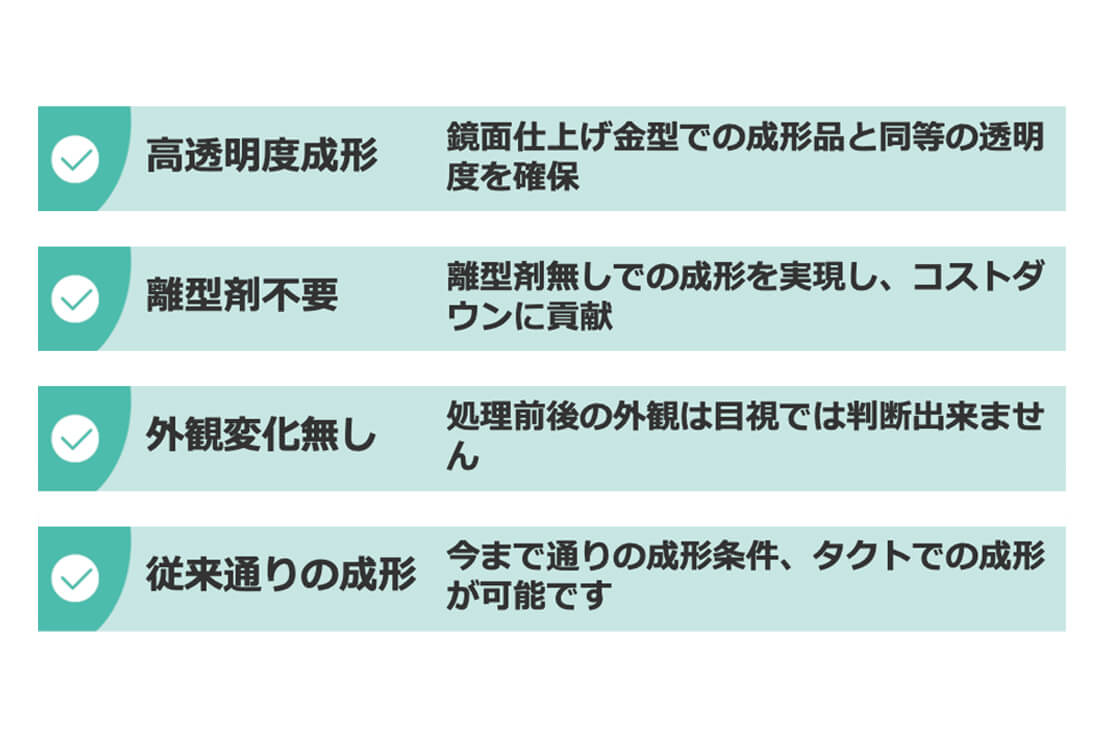
光学的特性
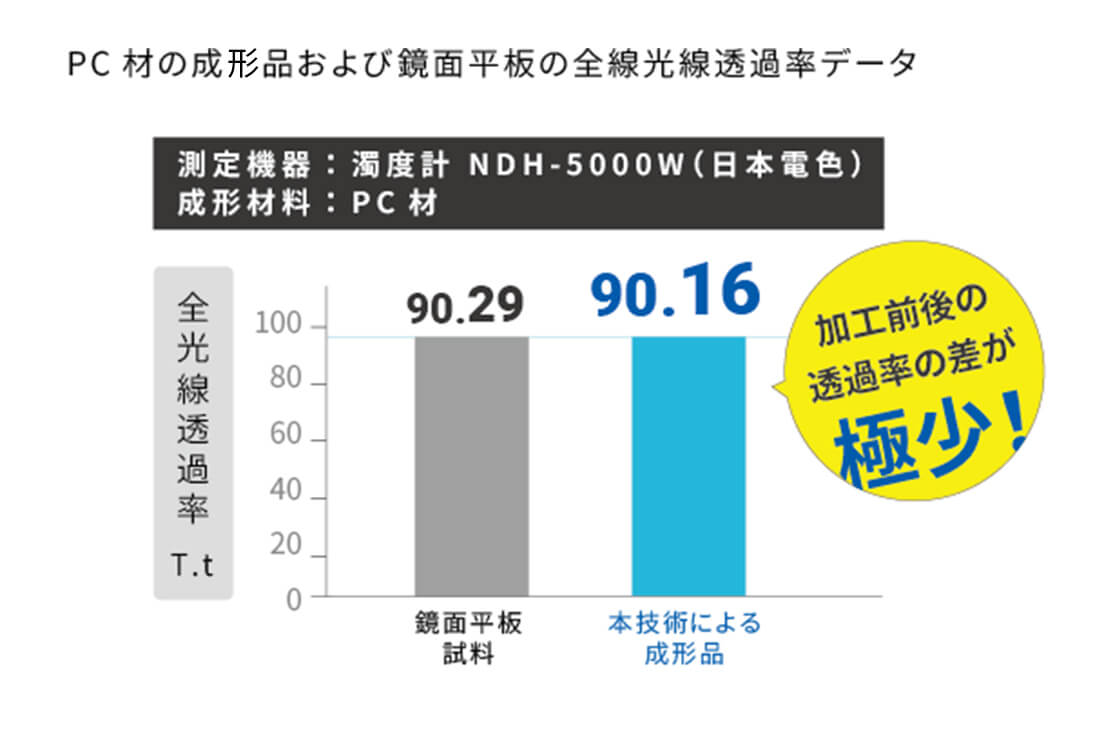
シリウスZによる金型鏡面仕上げ・研磨加工
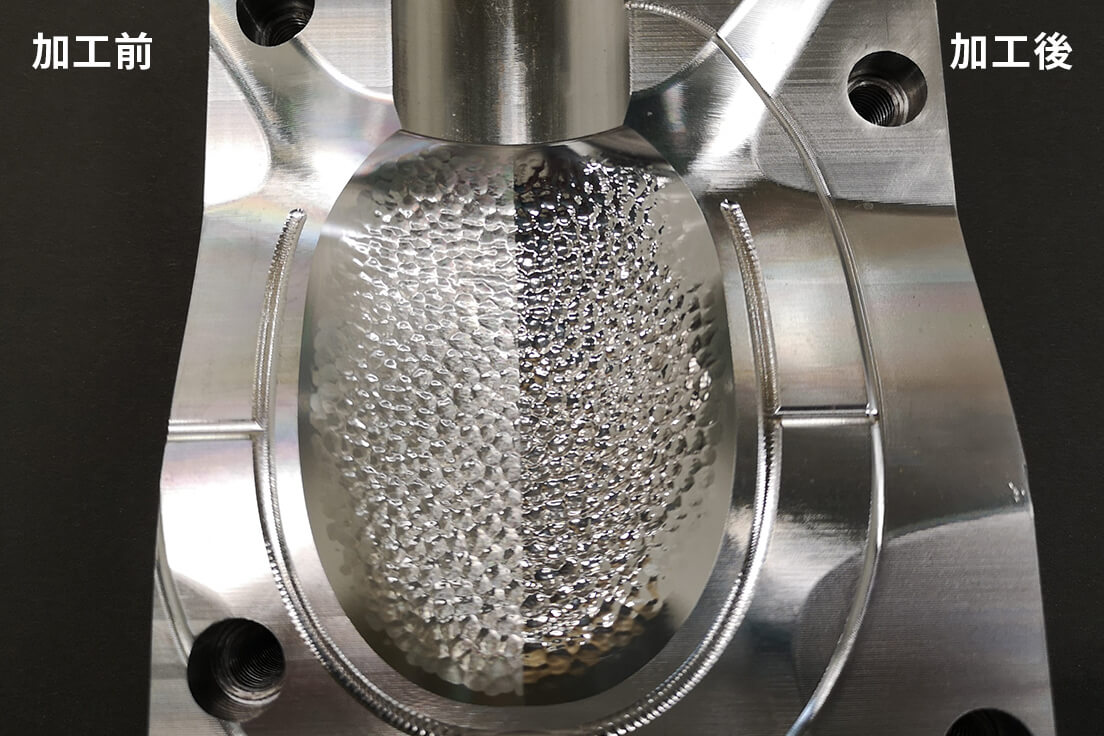
金型の鏡面仕上げ作業は手作業では大変難易度が高く、また時間もかかる作業のため、多くのお客様が熟練職人不足、作業の効率化を課題とされております。
当社では手作業での磨きで課題となっていた熟練職人不足、作業の効率化、作業者による磨き品質のバラツキを解決すべく、 3D形状、細溝、内径部への鏡面仕上げ・研磨加工が可能な「シリウスZ」を開発。下記リンクにてシリウスZならばどの様な加工物の鏡面仕上げ、研磨加工が可能なのかについて詳しく説明しております。
case 改善事例
成形不良別改善事例
ヒケ
ポリプロピレン製で400mm×100mm×H80mmサイズのウォッシャータンク成形時にヒケが発生しておりました。MKS処理前は樹脂を充分に流し込む前に樹脂が冷えてしまい、ゲートシール(ゲート部での樹脂の固化)が発生し、それがヒケの原因となっておりましたが、MKS処理後は樹脂流れが改善しゲートシール前に充分な樹脂量を流し込めるようになり、同時に離型性も改善したためサイクルタイムを短くすることが可能になりました。
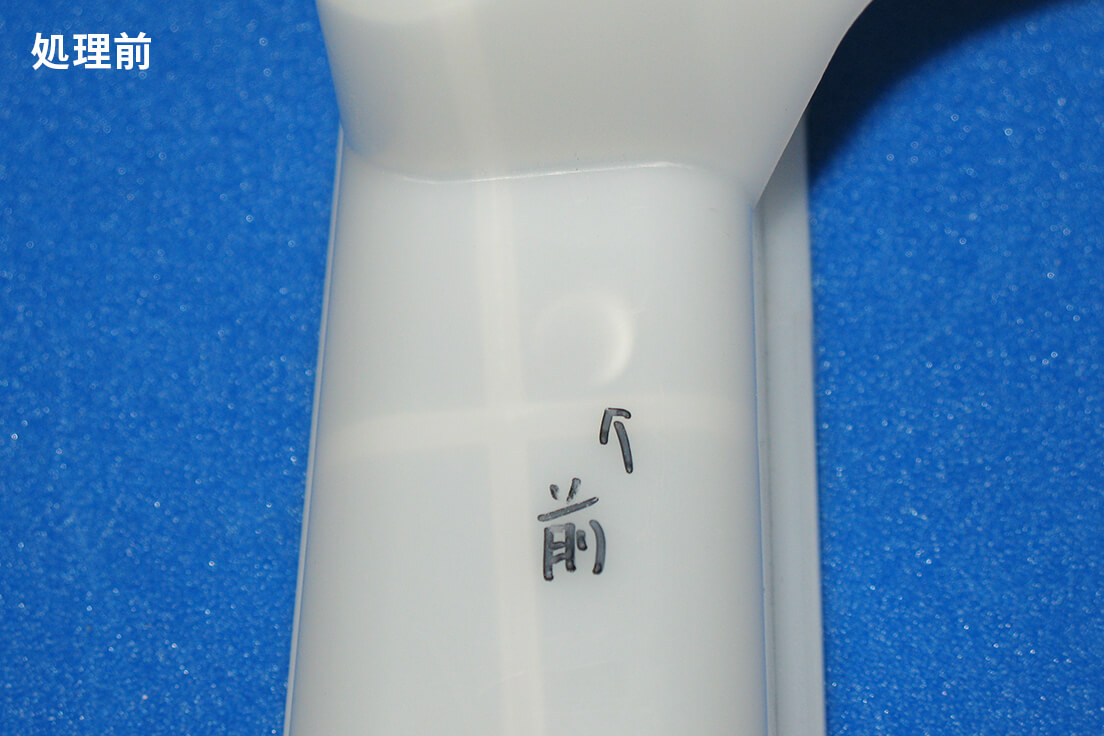
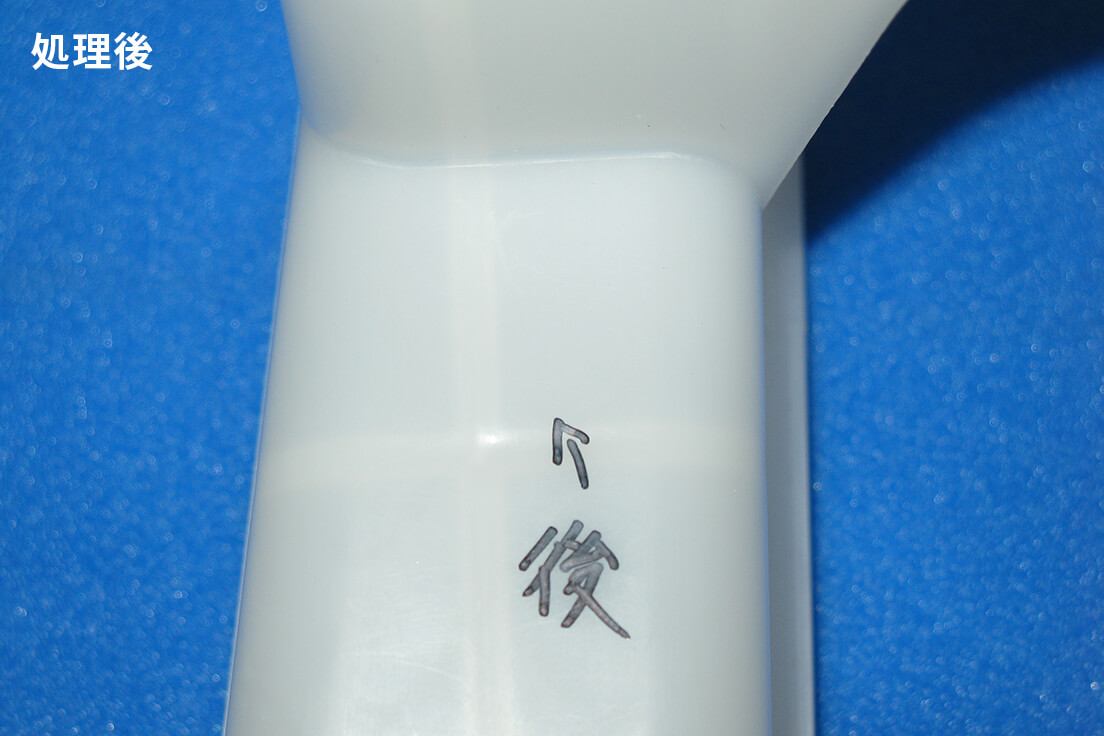
ショートショット
ポリカーボネイト製で800mm×200mm×H250mmサイズ、薄型湾曲形状の自動車部品成形品金型末端部分でショートショットが発生しておりました。射出圧力を上げると反りなどの別の問題が発生してしまうため、金型表面改質処理を実施。樹脂の流動性の改善によってキャビティー内の充填不足のみを解消し、他の問題の発生も抑えました。
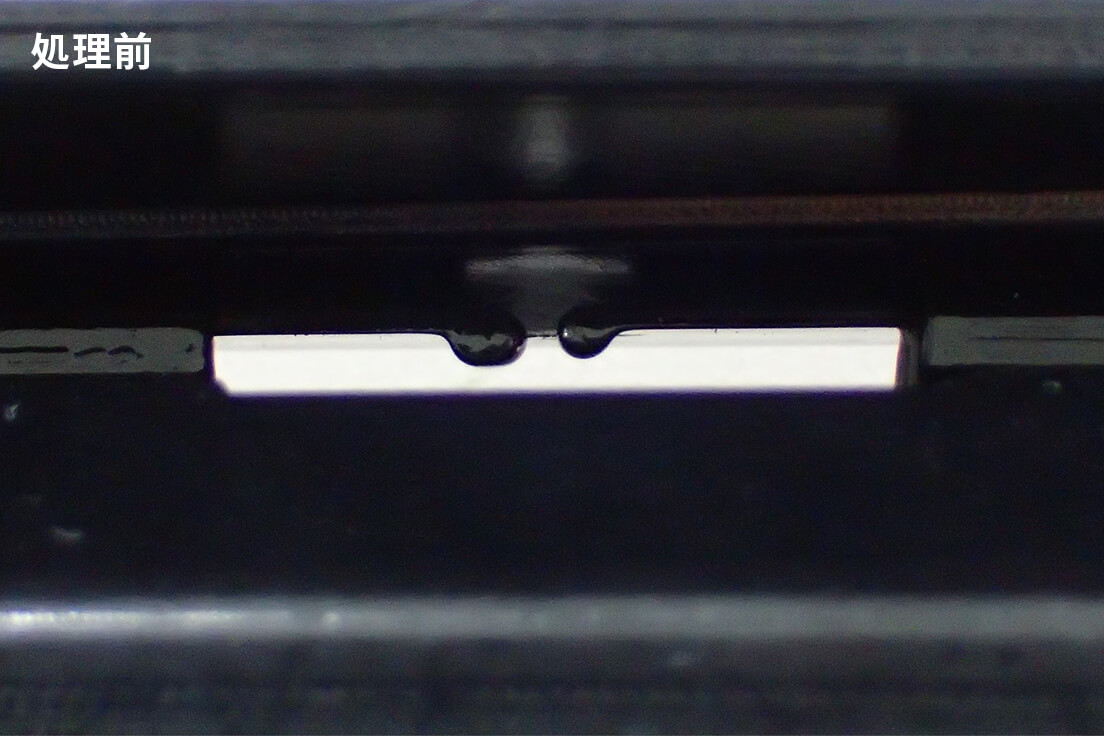
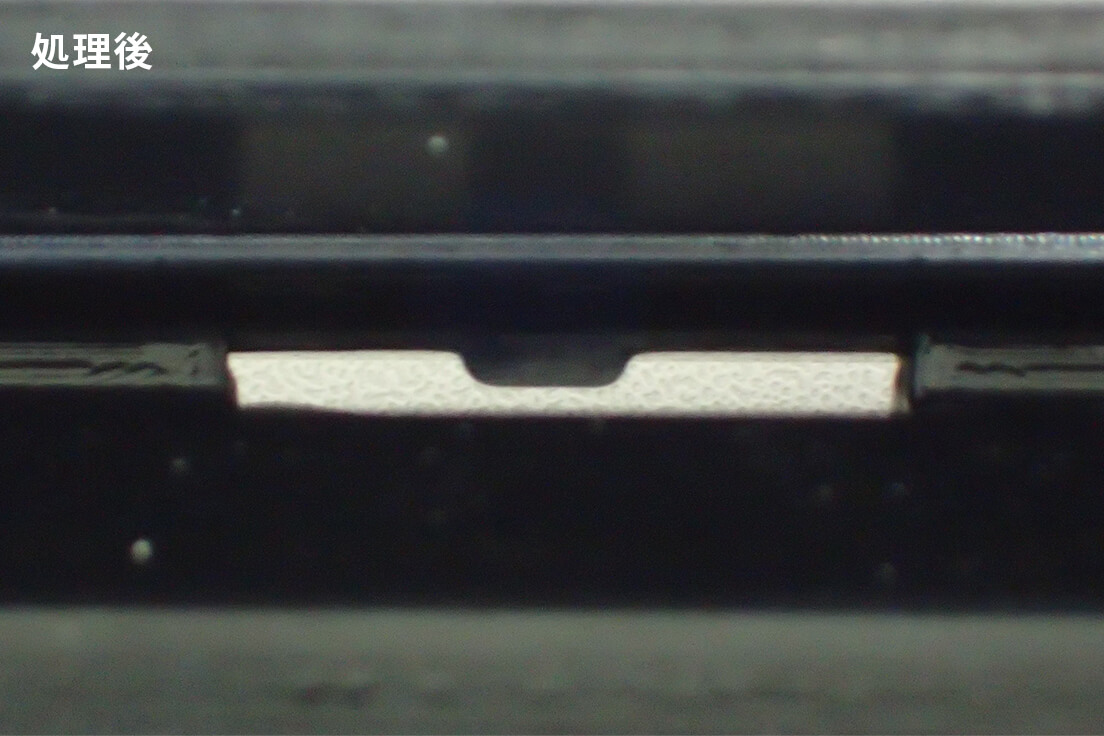
ボイド(気泡)
ポリプロピレン製の半透明樹脂成形においてボイドが発生。ボイドの発生が製品の外観不良となり不良率を高めておりました。ユーザーにて材料の乾燥など見直してみたが改善せず。金型表面改質処理後は、樹脂流れがスムーズになったことを活かし、充填量を増やし樹脂密度を上げることで不良率が大幅に改善いたしました。
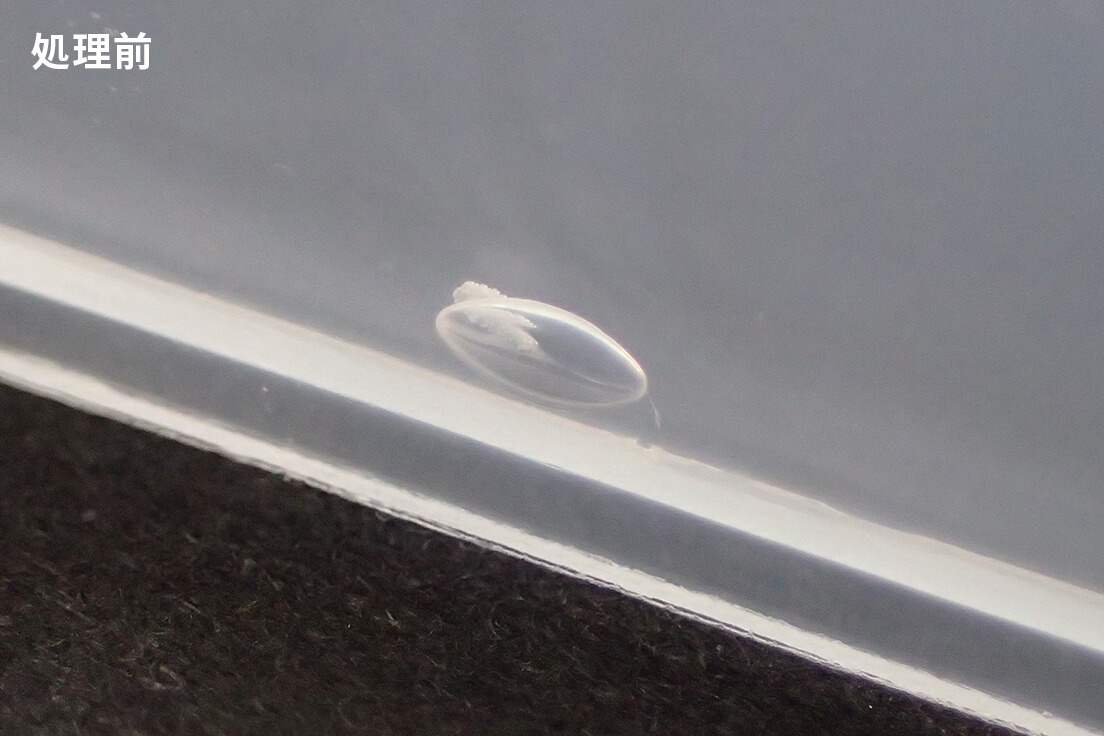
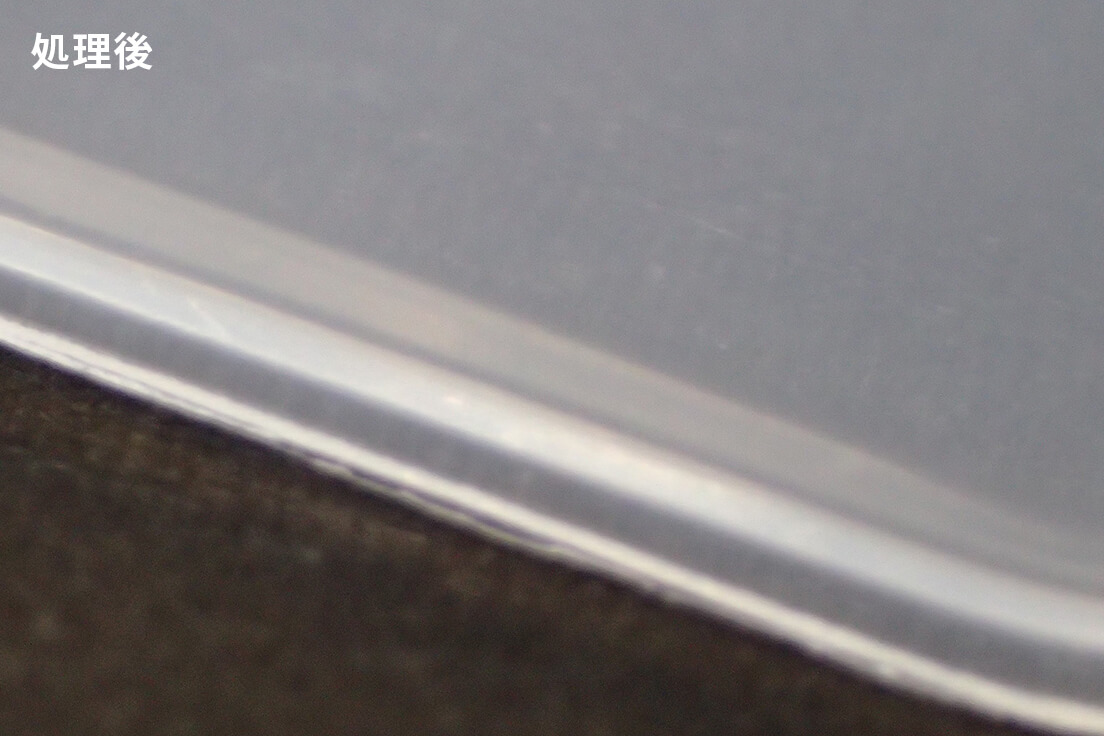
ブリッジ(しわ)
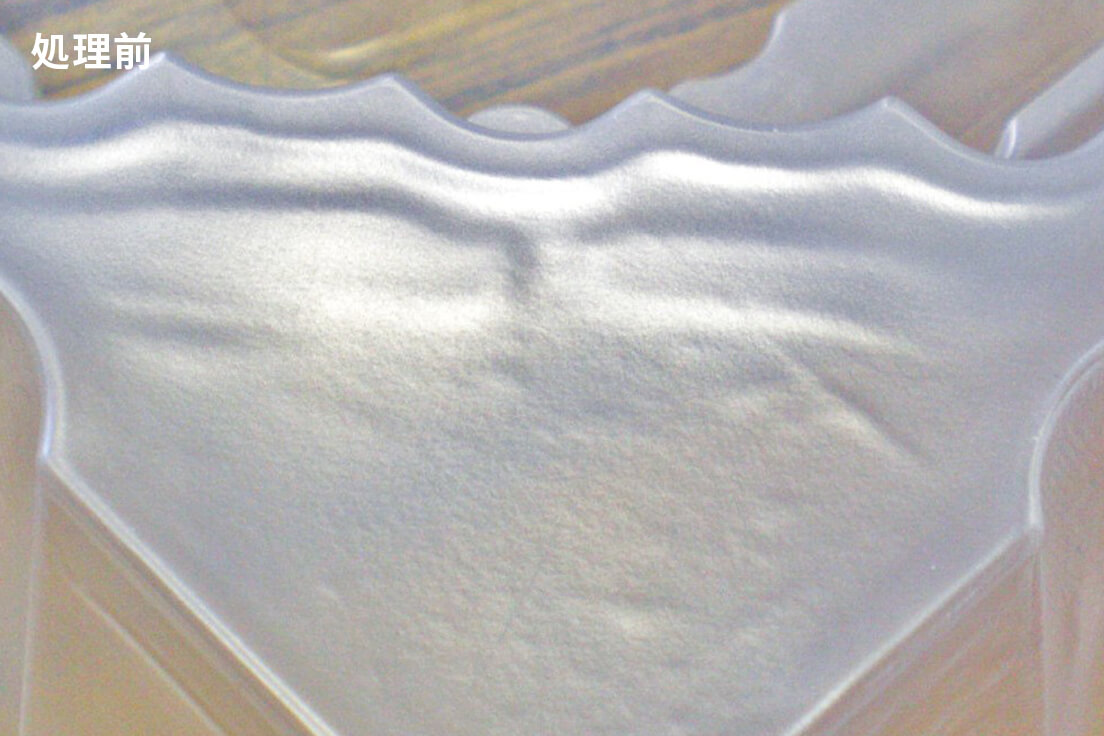
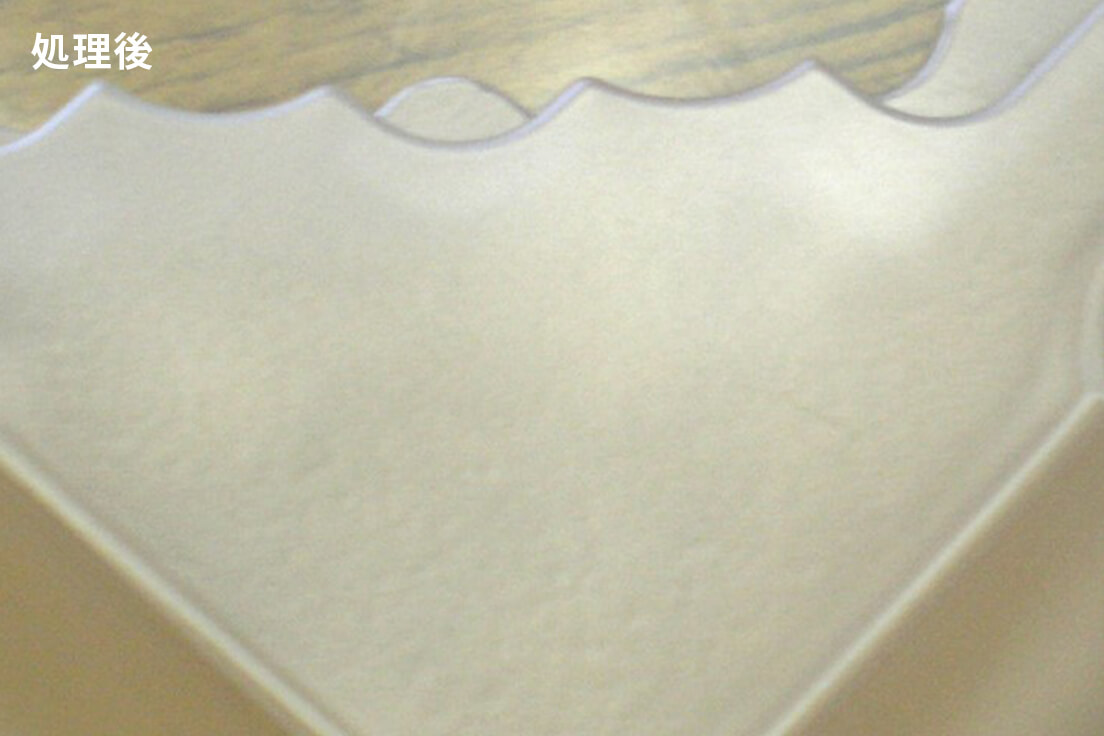
- 真空成形(成型) 材質:PP
製品別改善事例
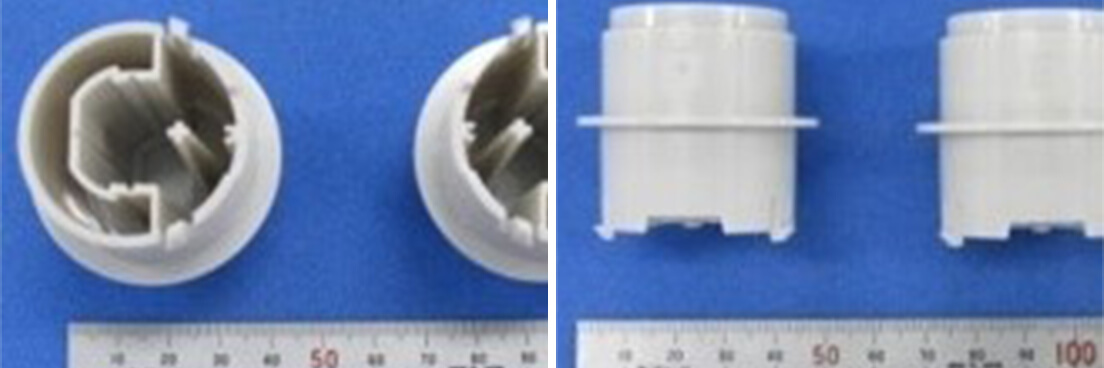
電装品ボタン
MKSの効果
- 樹脂流れの改善
- 型抜け改善(型温90℃で成形するが、10回前後で反り、歪みが発生していた)
- 中子への抱き付きがなくなった
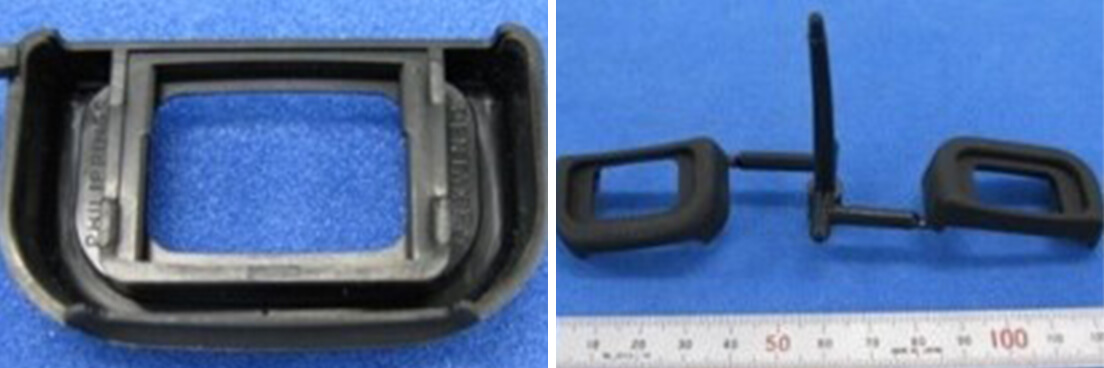
デジカメ部品
MKSの効果
- 4箇所のエジェクタピン跡が軽減
- 樹脂流れの改善
- 離型抵抗が減り反りの改善
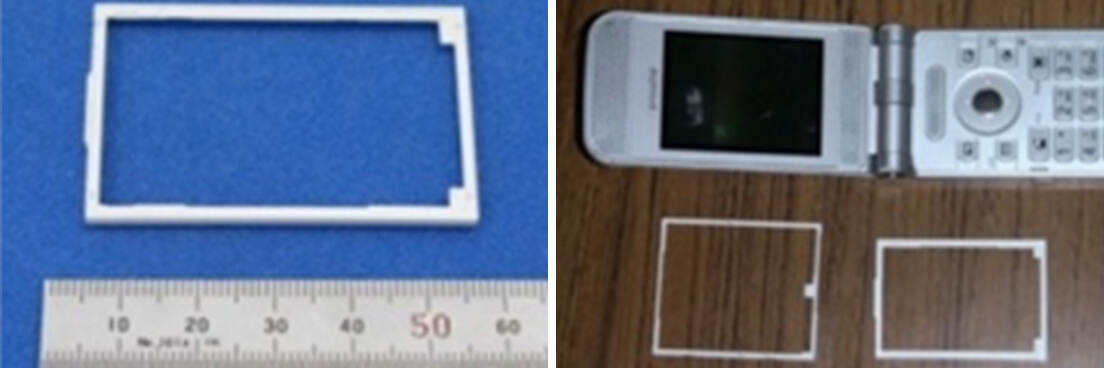
携帯電話液晶枠
MKSの効果
- 反り、歪みが解消
- 製品への梨地シボで外観向上
- エジェクタピンのカジリ防止
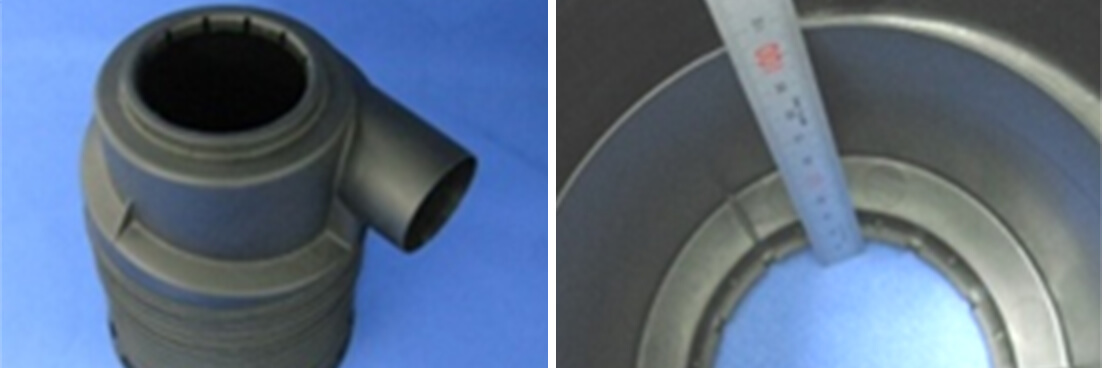
建機用サイクロン
MKSの効果
- 樹脂流れの改善
- 中子への張り付き改善
- 最大深さ87mmの深リブの抱き付きが改善し、量産が可能になった
携帯電話ケース
MKSの効果
- 樹脂流れの改善
- 型抜けが改善されてスムーズに成形
- 傾斜ピンにも処理し、カジリが改善
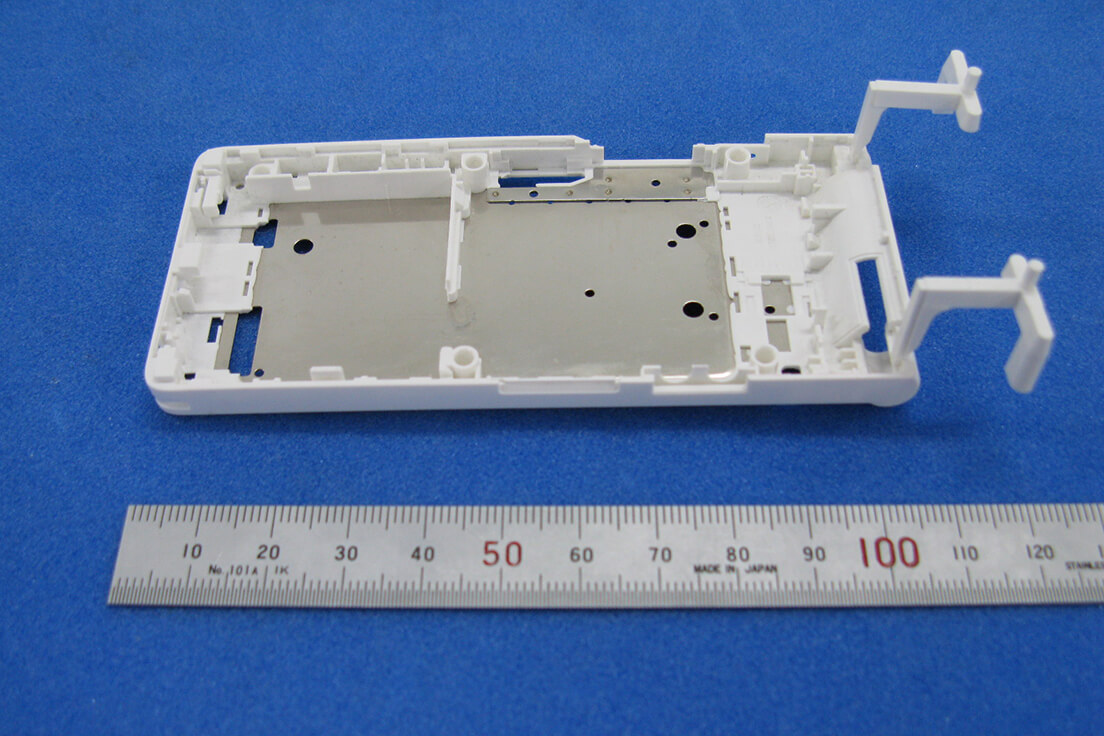
ボトルキャップ
MKSの効果
- ネジ部の型抜け改善
- 反り、歪みの発生無し
- 頻発していた成形トラブルが改善
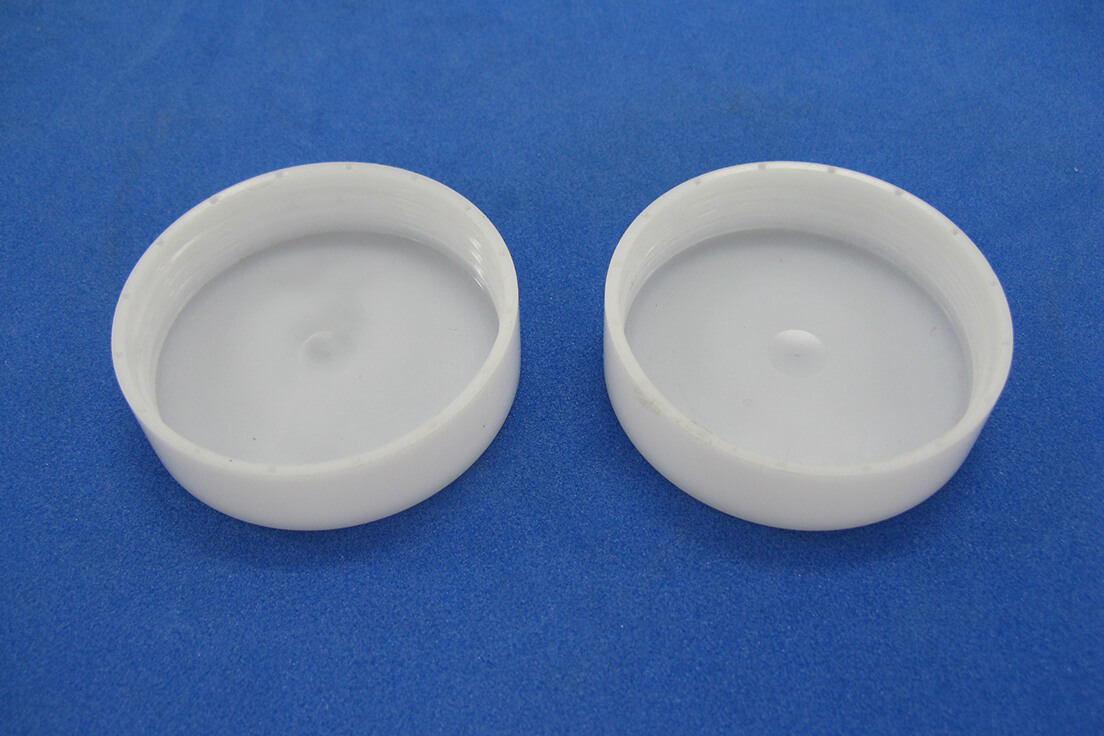
PETボトル(プリフォーム)
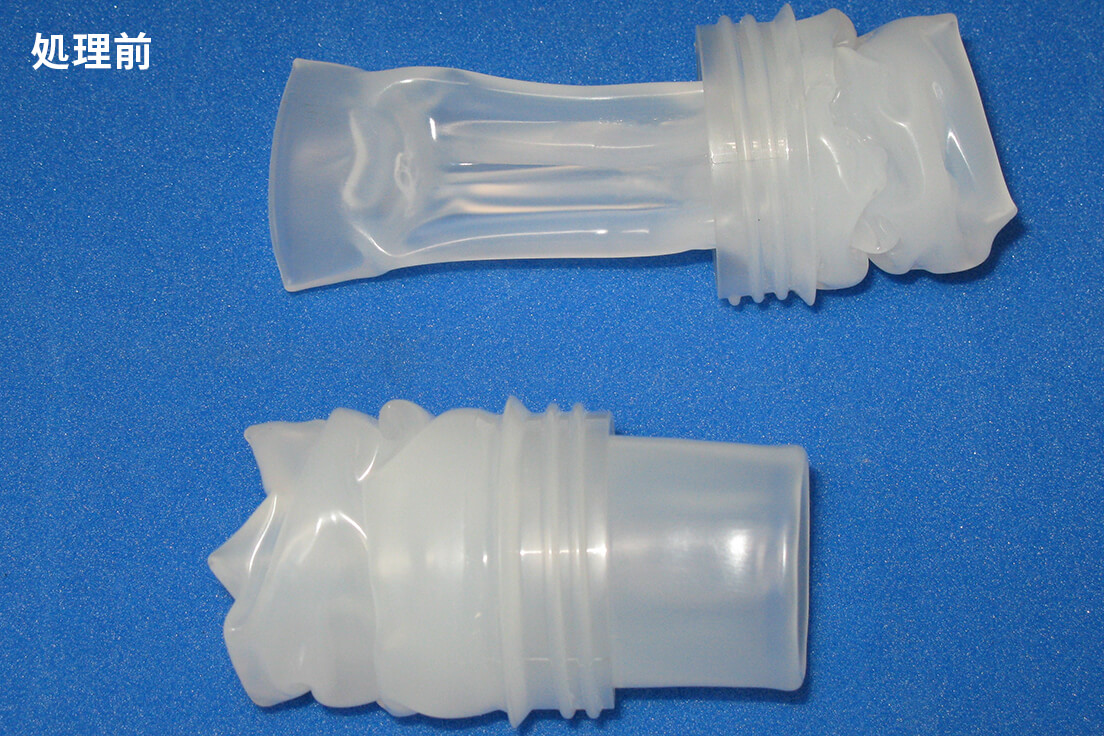
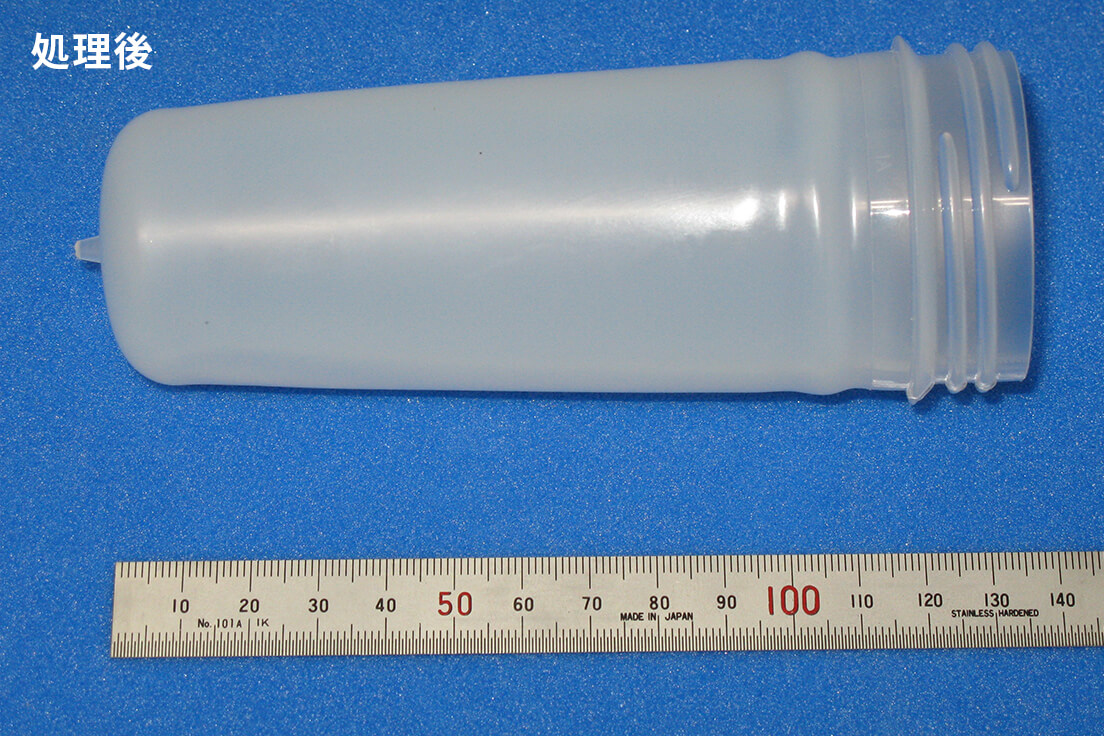
MKS処理及びGMT処理の受託加工に関するよくあるご質問
- 処理前後での金型寸法はどのくらい変化しますか?
-
代表的な寸法変化としては数μm程度です。
- どのくらいのサイズまで対応可能ですか?
-
重さ8トンまで処理可能です。詳細はご相談ください。
- コーティングとは違うのですか?
-
金型表面に微細な形状を形成することで機能付与します。コーティングとは異なり、膜形成する処理ではありません。
- 対応可能な成形材料は?
-
スーパーエンプラやガラス繊維強化樹脂など様々な樹脂材料に対応可能です。
- どの様に依頼すればよいのですか?
-
サンプル加工やお打ち合わせ後、金型をお預かりして処理致します。詳細は金型表面処理担当までご相談ください。
- 受託加工の工場はどこにありますか?
-
東京都江戸川区、茨城県稲敷市、愛知県小牧市の3エリアに受託加工が可能な工場があり、お近くの工場にて加工させて頂くことが可能です。
この用途・技術ページを見た人はこちらも見ています
お問い合わせ contact
不二製作所のブラストは多種多様な用途に使われています。まずはお気軽にお問い合わせください。
-
東京本社
-
装置検討・修理相談に関するお問合せ
03-3686-5104 -
部品・研磨材購入に関するお問合せ
03-3686-5806
-
-
名古屋営業所
052-703-2291 -
大阪営業所
06-6190-2323
※各営業所でもテスト加工可能です。